Ports & Marine

Projects:
Daru Port PNG
Feasibility Study and Detailed Design
Fraser Osborn (Now Fraser Lever) was appointed as the Lead Design Consultant to co-ordinate the activities of other specialist consultants such as geotechnical, bathymetric surveyors, sediment modelling and vessel simulation studies for the design and construction of the proposed Port in Daru, PNG.
The port was proposed for the export of concentrates from the Ok Tedi Mine and the export of condensate from gas fields currently being developed as well as import of fuels and general cargoes required for the operation of the 20 MTPA Ok Tedi Mine.
Fraser Osborn undertook preliminary design and capital cost estimates for all the bulk materials import, export, storage and handling facilities and engineering review of the proposed port design.
The port design is based upon an extensive bathymetric program including modelling of the operations of ships in the proposed shipping channel.
In order to control the initial capital cost, the channel and the port have been designed for staged construction and the channel depth would initially allow for the partially loaded draft of the vessels using the port.
As the port is developed for other minerals, oil and power projects the access channel will be dredged to accommodate the draft of more heavily loaded ships and additional facilities will be constructed. Total estimated cost for Stage 1 USD 350 Million.


Daru Wharf PNG
Fraser Osborn undertook a review of the existing trestle wharf at Daru and proposed a procedure which reduced the costs of repairs to the wharf by 35%.
Simberi Island PNG
Feasibility Study And Capital Cost Estimate
Preliminary design and capital costing of a land backed wharf for vessels up to 5,000T. Design included steel pile, steel framed wharf with concrete deck capable of supporting wharf loads up to 100T.
Preliminary design and capital costing of berthing facilities and infrastructure including power supply for floating ore treatment plant to be moored offshore during operation of the proposed island gold mine.
River Port PNG
Preliminary design and preparation of capital cost estimate for minerals dewatering, storage shed and conveyor systems including ship loader and port design for handling 1 million tonnes per annum of concentrates.
Cape Flattery Silica Export Port
Mitsubishi subsidiary Cape Flattery Silica Mines, exports around 2 MTPA of high quality silica. The materials handling system consists of a bucket wheel reclaimer, 5 kilometres of overland conveyor, a wharf and a ship loader. The capacity of the conveyor system is 2000 tonnes an hour of 99% silica.
The system consists of 5 conveyors feeding a slinger on the telescopic end of the ship loader boom.
The wharf was constructed using two self-elevating platforms to install rock socketed piles.
As part of the project Fraser Osborn undertook:
-
Design review of the wharf construction method.
-
Review of piling construction method and structural audit.
-
Report on preventative maintenance procedures.
-
Design and specification of berthing dolphins.
-
Design of land backed sheet pile wharf for unloading of service vessels up to 2,000T.
-
Design Changes to suit Australian Standards and access requirements.
-
Some years later. Fraser Osborn undertook the design of a new 800 TPH silica processing plant at the site and the land backed sheet pile wharf was used for supply of materials and equipment to the site (see photo below)

Cape Flattery Silica export wharf for the export of 2000TPH of 99% silica (above)
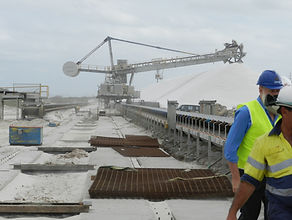
The Stacker/Reclaimer at Cape Flattery Silica Port
Curtain Brothers
Motukea Island, PNG
The Client proposed the 3,000 tonne ship-lifter concept. Fraser Osborn undertook the detail design of a submersible “wedge car” (to support the ship as it was pulled up the slipway) and a “transfer car” (to enable the ship to be moved sideways from the wedge car and parked in the nominated ship repair slot on the hardstand). The facility has been constructed on Motukea Island in PNG.
Curtain Brothers
Townsville, AUS
-
Extension of wharf length of Berth 10 to enable berthing of larger vessel.
-
Installation of ship loading crane on Berth 10.
-
Modification to slipway in Ross Creek.
-
Design of ship loading and unloading cranes.

Glencore Port Projects
-
Relocation of 25 tonne port crane from Berth 10 in Townsville Port to Berth 3 in Townsville Port. Project included provision of electrical, mechanical and structural engineering input into all aspect of relocation of the 300 tonne mass crane.
-
Finite Element Analysis (FEA) of original 40T capacity wharf crane to enable increase in capacity of crane for import of 2.5 MTPA of nickel ore.
-
Design of lead ingot lifter used world-wide to handle MIM 4 tonne lead ingots
-
Design of 27T capacity nickel ore unloading grab to fully utilise the capacity of the berth crane.


300T mass crane during relocation from Berth 10 to Berth 4
27T Ship unloading grab
BHP Groote Eylandt
Manganese Export
GEMCO uses front end loader recovery from ore stockpiles to export around 2MTPA. The feed rate to the ship loading conveyor system is between 1,500 TPH and 2,000 TPH.
The Ship loader facility product ore reclaim hopper car which can be controlled in both operation and position by the FEL operator from the FEL cabin was designed by Fraser Osborn.
Other projects at Groote included design of repair and reconstruction proposal for land backed wharf and barge unloading facility for general cargo.


Simberi Gold Project
This project included 4000 tonne heavy fuel oil ship unloading storage facility and dispensing system to a 10.5 MW power station.
